Friday, March 31, 2006
Where am I Going, What is this Handbasket?
Turns out I had to pay for electricity (which I did because I want my laptop) because the festival has a special event from 7-10 tomorrow night! I am required to be there, required to be open, and required to have lights which I did not bring. I am loathe to go to Home Depot and buy a bunch more lights because I already have lights in Atlanta--I bought more lights for the BMAC so I have lots and lots of lights in Atlanta right now. I also will need to buy some kind of support system for them as I left that in Atlanta too. Oh joy. If I really wanted to piss off the festival organizers and never get invited back again I could just not be open tomorrow night and save myself a couple hundred bucks. Sadly I am not that kind of a professional.
So a day which was going to include nothing more than a little clothes shopping, a pedicure and a leisurely stroll through the Apple Store (we did Fry's yesterday--what a treat) with a quick set-up at the end followed by the Midgetmen at the Flamingo Cantina now has the extra added joy of a lighting emergency. Oh yes, and a nice dinner tomorrow night with Lize and the girls is shot to hell. Oh well, there's always Sunday night... late... after breaking down the show... maybe not.
Thursday, March 30, 2006
Austin Texas!
Coffee is Green Mountain Sumatran Reserve in an elegant black mug. Most importantly it is coffee from a Keurig coffee maker. Oh my. This is technology at its finest--exactly what I would expect to find in Austin. A fresh, hot cup of coffee in five seconds with no clean-up. For the ecologically and fiscally conscious there is a MY K-CUP reusable K-Cup filter assembly which allows you to use your own coffee (some clean-up there). The default is little individual packs of coffee that look like creamer containers that you put in the coffee maker and throw away after brewing. Music is from the dvd Aladdin which Jessie is watching on the Big tv.
It is only bested by the wireless access I have from the Linksys WUSB adapter I borrowed from my friend Bryon. (He and Vanessa are also the owners of the coffee maker and our hosts for the next few days.) So for those who need to know, there is a wireless network adapter that plugs into a USB port on your computer and it can be as fast as a regular network card. It is also a lot cheaper and easier to install--as a USB device it is plug and play--than the internal solution. So I am off to Fry's today to shop. Heh. Like I needed an excuse.
On the glass front, because I am in Austin I am obviously not in the studio today. However that does not mean I am not working! I got a call from two galleries yesterday whose orders I shipped before I left. One called to report four pieces broken in shipment, bummer. So I call UPS today to get the breakage investigated and reimbursed. Fortunately the pieces were all Archetype Industrials so I can easily replace them when I get back. The other gallery wants me to send them a sink on commission. They carry two other artists' fused glass sinks and when I met the owner at the BMAC she was very interested in having one in Morceaux de Verre. I have been wanting to do another one and now I have a reason!
Finally, I begin work with my new web designer today. Time to get that website up and going and boy am I ready! In fact, I think I will post this and call to talk to him right now.
Monday, March 27, 2006
Let the Week Begin
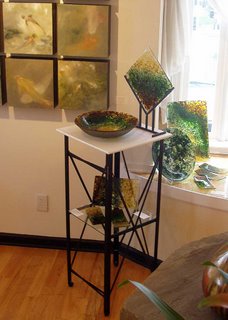

Leaving in a couple to snag some pieces from Creative Spirit to pad out one of the gallery orders I am shipping today and then up to Taylor Kinzel in Roswell to break down from Saturday's trunk show. The show was great. All three of us sold a good bit of work and I took on a small commission too.

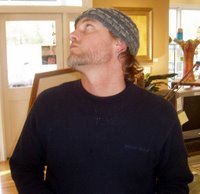
And on the subject of the new website: Friday I got a thank-you-for-your-business letter from the company that is going to develop it for me and in it was a little box of chocolates! The chocolate was from another little company in the same town as the website developers (Rexburg Idaho). I was very impressed and the chocolate was very good (Dave, Jessie and I scarfed it down Friday night). Last night I got them the navigation diagram and all the content for the first eight pages. I am eager to see what they come up with (and very relieved that it is not me doing it!).
Friday, March 24, 2006
The champagne is chilling...
Today I sorted all of the work I have done in the past two weeks into piles for two of the three gallery orders I need to ship Monday, for the glass trunk show I am doing at Taylor Kinzel Gallery tomorrow, for the Austin Fine Arts Festival next week, and for the gallery in Dallas where I am going to drop off a delivery on my way to Austin. Tonight I need to fuse the pieces for the third order which is scheduled to ship Monday...
I am so exhausted right now I cannot even see straight. I spent two hours this afternoon at Taylor Kinzel setting up for the show. I will go back tomorrow morning at 10:00 and stay until 5:00 when I break down my display and pack everything up to come home. Tomorrow I also have to slump the load I am fusing tonight. And I think I have either one or two loads of Archetype Industrials scheduled to slump Sunday. Frankly I do not have the morale to look that far into the future to see.
Now for the good news since I got all the whining out of the way. Today I received notification that the Museum Shop of the Art Institute of Chicago will be carrying one of my pieces in their fall catalog this year! And this is an art glass piece--not the Archetype Industrials. Now if I can just remember the formula I used to make it so I can replicate it 50 times for the initial order...
The champagne is chilling in the fridge, Dave has gone to pick up dinner, and I am going to allow myself to relax and celebrate my week... at least for the next 37 minutes.
Thursday, March 23, 2006
A Technical Advance
Don't get me wrong--Thinfire is a wonderful product. But to have to use it for every firing, and to have cut enough to cover the entire shelf area in Big Bertha (almost 6' X 3')--because I always plan to fill her all the way up, but sometimes I run out of time and have to fire with gaps--is both labor and cost intensive. Then there is the clean-up: After Thinfire has been fired it turns from paper to dust held together with a fragile webbing. If you scoop carefully sometimes you can get it all up in more or less one piece. If you end up having to sweep up bits of it (90+% of the time), it sticks to the shelf and makes a dusty mess.
So how did I break this vicious cycle? At the end of 2004 I bought a large ceramic fiber board to use as a kiln shelf (Duraboard HD... I think). I scoured the warm glass posts and archives to see how to prepare it for use as a shelf and to find out if I could fire bare on it or if I needed to use fiber paper (Thinfire) or fiber blanket. The answers I found were mixed enough that I just went ahead and used Thinfire for safety's sake: The last thing I wanted to do was fuse a glass piece to my brand new soft shelf and have huge chunks pull out of it when I lifted the piece up.
A couple of weeks ago I broke a corner off of this shelf as I was maneuvering it back into the kiln after a deep slump. So a couple of days ago I figured, what the hell, that corner is already munged up anyway, why not try to fuse on it to see if the glass sticks. It did not! I am going to do more extensive testing, but it looks like I can fire bare with equanimity at my fusing temps. This is going to speed up my production cycle and make my studio less dusty and less harmful to my lungs. And cheaper, did I mention cheaper?
Wednesday, March 22, 2006
Computers, Can't Live with 'Em, Can't Set 'Em on Fire
The kiln is cooling from yesterday's firing and I am losing my faith in computers--I mean, it must be the computer in the kiln that is the problem. It's *always* the computer that goes wrong. (Postmodernism. Yep. Dave: "You keep usin' tha' word. I don' think that word means what you think it means.") Anyway, I could have used 2-3 more minutes on the high soak. The day before's fuse could have used 1-2 more minutes. This is the same schedule that came out perfectly (with the same piece composition and configuration) just a few days ago. The only thing remotely different--if I were to look for a cause other than the computer--is the quantity of glass I am fusing.
Yesterday I was so giddy from my brush with fame (and finally getting the book contract) that my afternoon was completely derailed. I was still putting the kiln load in when Dave got home at 5:30. So instead of packing it to the gunwales (pronounced 'gunnulls'... isn't English great?) with unallocated pieces that I could use for shows and art fairs--and taking an hour or more to do it, I just fired exactly what I had scheduled and it was a smidge emptier. Whatever. I am done fusing for the week so I will just have to note the results in the firing log and come back to the problem when I get back from Texas.
Today I cut, grind and begin slumping the umpteen gazillion sushi plates that I fused over the past few days. I have got to buy more of those molds. Right now I can do either 12 plates or 4 platters and four plates at a time and the molds do not take up even half the kiln. So I fire half empty and am filled with guilt at the energy I am squandering to heat the whole kiln--as well as the extra time it takes to get it done. *sigh* I just got an order from Bullseye. I really don't want to order again (come to think of it I haven't even paid for the last order yet) but somehow I am almost out of #2 neo-lavender opal frit, running low on several other colors (what is it going to take to accurately predict how much of which colors I will use?) and I have less clear irid than I thought I did.
Today I FINALLY get my accounts receivable updated and my web content materials organized and shipped out. Having someone else with the responsibility of designing and implementing the website is a tremendous weight off my mind. Now I just need to solve the shed and computer problems and I will be set. Mass-marketing efforts are put on hold till after the book is finished. I am stupid but not suicidal.
To get me moving, "Ronnie and Neil" by the Drive-By Truckers just came on the Pod. Now there is some music I can be proud of.
Tuesday, March 21, 2006
It's Official!
Post-Modern Operators
Yesterday was a big day. I virtually met a woman (talked on the phone) who makes natural soaps and body products and supplies one of the galleries I am in. The gallery owner recommended I call her about information on avenues for expansion into the department store/large catalog marketspace. The soap and personal products are her weekend gig (in addition to two small children and a husband). During the week she is a product stylist with--again--her own styling business. She was a font of information and in addition to all the good tips she gave me, she gave me one lightbulb-exploding one. We were talking about tradeshows and she recommended that I do the Atlanta Gift Mart in January--not with all of my work, just the Archetype Industrial pieces which I am ready to take to a new market. We talked a bit about booth design and I said I was really happy with what I did for the Buyer's Market of American Craft. She said it was good I had developed a strong booth design as establishing corporate identity is key in this space.
She went on to say that a great e-commerce website is also crucial (and her soap site is gorgeous). I had to admit that my website pretty much, well, no way around it, it sucks. And there is no e-commerce in it at all. Now here is the lightbulb exploder: She recommended giving photos of my booth to whoever does my website so they can see how I present my work and design the site to match. Wow. It is so obvious and makes so much sense. I have struggled (and brought hell to the lives of friends and family who have tried to help me with my website) for the past three years trying to build a site about who *I* am and what I see as the roots of the studio (Siyeh Peak/Pass, Glacier National Park, Montana) and I completely ignored the work. My work is bright, primary, visceral colors, and my websites have been muted, soft earth and nature tones. Maybe that reflects me, but it does NOT reflect my work.
We talked a bit more about website design firms and she pointed me to BizAtomic. I filled out their on-line form and Nicholas called me to talk over my needs. After about an hour of his time, he said that maybe their service were of a higher level than I need right now. The only e-commerce I want to be able to do is have galleries with wholesale accounts be able to login, see the current catalog and order on-line. Most of those accounts have Net 30 terms and even those who don't I need to call about scheduling anyway so I can get the credit card info then. So I don't need to be able to process payments on-line.
Now here's the kicker from them: Nicholas said that they often recommend another company, EZNetTools, for customers who need fewer features and would like to keep the costs down a bit, but still want excellent quality and service. He gave me their phone number and the name of a person to talk to, told me their monthly e-commerce hosting fees, and said he would call me this afternoon to see how it went and what I decided to do! He said that I can always start there, and if my needs outgrow their ability, I can move to BizAtomic. And it's not even like they are friendly rivals in the same place: BizAtomic is in Florida and EZNetTools is in Idaho.
So I called EZNetTools and the long and short of it is I have hired a web development company to create and host an e-commerce site for me with everything I had hoped to have this year for a price I can afford. And the process was so slick! As we finished talking about the costs, etc., my sales rep gave me a url that began with his name, and when I went there, I saw my quote in detail! As I read it over I saw an item that wasn't right and when I brought it to his attention, he corrected it and it disappeared from my screen. I printed it out, signed it and faxed it back, and we start development today!
I told Dave this whole story last night and, nerd that he is, he kept going on darkly about how they were all post-modern operators ala Bruce Sterling: constantly looking ahead for the next angle, the next deal, and going to take me for all they could get. I don't think I ever got across to him that at least the woman I talked to first gave me all the information and advice free for nothing--no expectation of future gain.
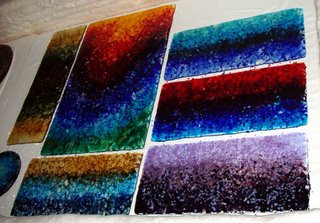
On other topics (because of course that isn't all I have to do right now) I fused a full kiln load yesterday and it came out great. In the load are a 15" bowl, 2 11X7 sushi platters (fused together) 20 sushi plates (fused in sets of five), 4-8" plates (fused together), a 7.5" dish, and a 16X24 hanging panel. Whoo hoo!

Monday, March 20, 2006
Monday, Monday...
Dave is home from Austin and he has wireless so that means it is the internal wireless modem in my laptop that doesn't work. (A break for a rant) This is a two year-old Compaq laptop. The battery lasts 10 minutes when it is unplugged and now it is no longer wireless. To fix these two things will cost me about $250. And fix them I must as I am about to head off to Texas for a show and I will need both battery and network. This is after replacing the power cord in February in Philadelphia ($80). I am reaching critical mass on the amount I wish to spend on this machine. It is slower than dirt and manipulating any image files takes FOREVER.
On the other hand, I do not wish to buy another windows machine. I am ready to move back to Mac (my first laptop was a Mac DuoDock in 1992). But I am not financially ready for that move (machine and software), nor do I have the time right now to invest in the OS ramp-up. It is a great quandary. There is also the whole issue of what Mac to buy: After many years in winblows I know the processor speeds and types, the amount of RAM, etc. that I should get. The Mac numbers in comparison seem so... small. The processor speeds in the mid-range are 1.5-1.6 GHz. Windows machines are in the mid 2's now. Yes, I am more than willing to believe they are less efficient, but it makes comparing difficult.
Okay, I found some common numbers with the same processor (the new dual core thingie). I built a Dell system and an Apple system with *exactly* the same options wherever possible (different screen size and battery life) and the Dell came out to be $300 more! Of course either option was over $3,000. Shed, laptop, shed, laptop: Both are necessary business components and the shed is also a necessary personal component to keep my husband sane (stuff is everywhere right now--though not in the cat's bathroom closet! See Stranded in the South for details on the great electronics purge). So I will do what I always do when faced with a technology purchase choice... Help, Johnathon!
As it is Monday I am cleaning up details of work left undone on Friday: Orders to place, bills to pay, testimonials to write... and a follow-up call to the Publisher to find out if they still want me to write a book for them! I got the operations manager and she passed the contract on to the publisher (an actual person with that title, as near as I can tell) a few weeks ago and doesn't know what the status is. I said time's a wasting and Neiman Marcus waits for no man so as tempus fugit, what is going on?!? Someone will get back to me. The writing task (not to mention this blogging) has an impact on the laptop issue too. (I do not use "impact" as a verb. Alexander Haig was just flat wrong.)
I worked all weekend fusing 25 sushi plates, a 16X24" hanging panel, a sushi platter, 2-8" dishes, a 12" bowl and a 16X13 S curve platter on Sunday and slumping 10 sushi plates, the sushi platter, one dish, the bowl and the S-curve piece on Sunday. Now I need to run the hanging panel to Dixie Glasshoppers to be drilled and then I need to fill the kiln with another fuse load.
I am in a glass trunk show at Taylor Kinzel Gallery this weekend and need to get a lot more new work done--interspersed with the three gallery orders which need to go out before I leave for Texas next Wednesday. Gurk.
Friday, March 17, 2006
One Damn Thing or Another... and a Good Idea
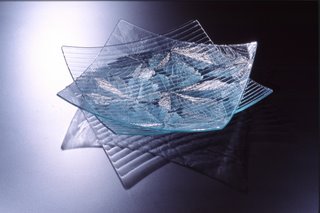
Anyway, back to the internet situation for a moment. Either the router's wireless access is kaput or my laptop wireless network card is fried. I will have to wait till Dave gets home and there is a larger sample of computers to test to determine for sure. In the meantime I have a cord, am not happy about it, and wanted to share that state.
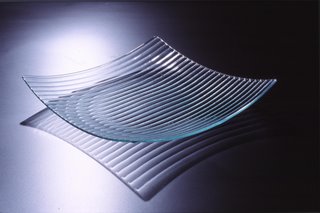
"I Ran" by a Flock of Seagulls ushers in the idea: I am ready to supply the masses and move into the department store market. Oh not for everything I do. No, I want to get the AI pieces out to the world. I LOVE them. They are all made from machine-cast glass which I cut, grind, slump and combine into sets of functional ware. I make everything from sushi sets (I can now even do the soy cups) to dinnerware. There are sets of tapas plates, rectangular serving trays in a variety of sizes, 8", 10" and 12" square plates... I could even do the Seder sets in them now that I have created the molds.
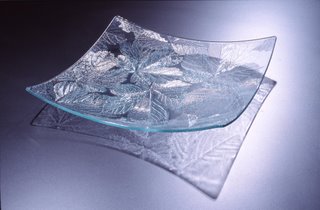
Even more important than the issues of demographic interest and cost is the production question and part of the reason I am not really making a living as a production glass artist is that I can make far more than I sell. Even though I am now in (or will be in once all the orders I am working on have shipped) 24 galleries and do five retail art fairs a year including the One of a Kind Show in Chicago (a big one) AND get an average of four-six large commissions a year, I am still not producing at full capacity or even close to it.
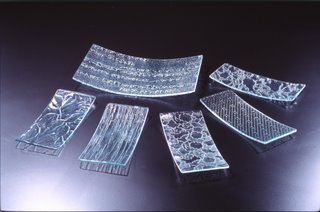
Of course I would have to get another kiln for really big production, and I would totally take over the garage for glass and mold storage and new kiln placement. The last time I bought glass for these pieces I got four cases, 2000 lbs of glass. For serious production I would need to double that. And I would want to store it as close to the drop-off point for the shipper as possible. Last time I moved all 2000 lbs one sheet at a time over two days all by myself from the parking pad outside through the garage and into the studio. Boy was I sore! (On the plus side, this kind of a workout obviates the need for a gym membership and is free.)

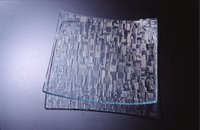



Thursday, March 16, 2006
Am I an Artist?
______________________________
Wednesday, August 24, 2005
An auspicious day to begin a new artist journal. I just ordered two books from A.com on being an artist. This was in response to a post about self-doubt by another glass artist on Warm Glass. In it she talked about the inspiration/motivation for her pieces—their spiritual history if you will. I read it and realized that I don’t have a spiritual history or a motivation for my work. It is beautiful, therefore it is. Does that mean it is not Art because there is no meaning behind it? Should I start trying to make art based on things I feel and care about? If so, I will become an environmental artist, and most of that work I find schlock. It also doesn’t lend itself to what I like to do. Many of the artists on the list don’t like production work—they just want to do inspired art pieces. I like production. Does that mean I’m not an artist?
______________________________Well, it sounds like me. All except that part about most environmental art being schlock. I have no idea what I was thinking there.
Fortunately today I am in a more secure mental state (probably because I have been journaling-for-the-new-milennium, i.e., blogging, for the past few months and production work has been really going well). So I put out there that I wrote this, and now I delete the file, delete the icon, and move on to getting my child ready for school and finishing my firing schedule for my upcoming trunk show (3/25-26), my first retail fair of the season (The Austin Fine Arts Festival in Austin, TX 4/1-2), and the orders for seven new galleries that I have to get out by the end of April. Did I mention that I am writing a book?
Wednesday, March 15, 2006
For Barbara
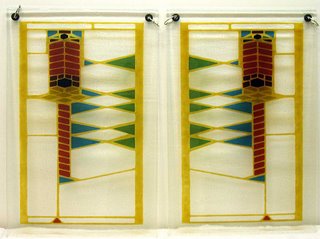
Barbara, you come and hang in my studio for a weekend, and I'll show you how to get these REALLY crisp lines. (Then I'll come to your studio for a weekend and you can show me how you lay out your lovely figurative layerings.)

The Dinnerware

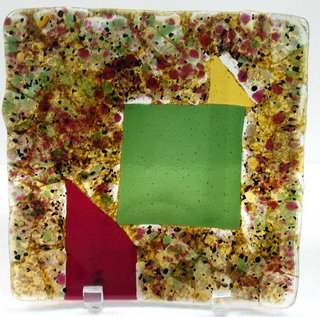

Mixed Blessings
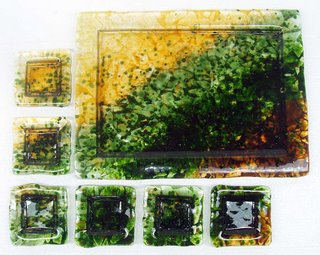
Coffee in the
The first news of the day, which is overwhelmingly good, is that the Seder plates are not ruined and neither are the molds. 1425+degrees and no kiln wash. Must be ceramic board and I may start experimenting with fusing directly on it (it has a really smooth finish). The downside is that the board I have is only 1/2" thick and therefore not sturdy enough to be a shelf. One of the paisleys is definitely ruined, and the other might be. The dinner plates look to be fine (whew!).The bad news of the morning is that I did not get into the 57th Street Art Fair in Chicago in June. I am not too surprised: They have a grandfather system which means that if you get accepted once you get to be in forever without jurying again. This limits the number of new artists accepted to about 50. Last year when I looked, they only had three glass artists total--none of them with kilnformed or functional work.
I am also still wait listed for the Dogwood Festival. I understand I am the first person on the waitlist in the glass category so all is not lost, but the deadline for payment of fees has already passed so my chances are slim. And finally, I STILL have not heard back form the Publisher regarding my book contract. I sent them a gentle reminder that I am WAITING earlier this week and they have not yet replied. How swiftly the winds of schedule change from over to under full.
I end with my glass all the way full: If a bunch of things drop off my schedule for the year, it leaves me with more time to experiment with new techniques and ideas, work in my yard, and laze in the hammock reading. There is no bad-case scenario there.
Tuesday, March 14, 2006
Pride Goeth Before a Fall
So I put the last two plates from my dinnerware commission, the last Seder set and two unassigned 12" paisley plates in the kiln to slump. I decided to be tricky and put in two top-temp soaks to mimic the extreme effort I went through manually last night. What I *meant* to do was ramp up to 1225 at a moderate rate, soak for 20 minutes and then ramp to 1265--again moderately, and soak for another 20 minutes.
I *meant* to set the timer so I could check towards the end of the second soak to make sure it was enough, but I forgot. But it would not have mattered, the damage would already have been done when the timer went off. And as it was, I went down and looked in before the second ramp was done.
What I actually programmed into the kiln computer was a ramp up to 1225, soak for 20 and then a ramp to *1465* with a soak for 20... When I went down to check to see how things were going, the kiln was between 1425 and 1445 degrees. I don't know the exact temp because I freaked out when I saw it and immediately turned the kiln off and whipped up the lid (I have asbestos gloves doncha know). Everything was glowing an evil cherry red (pieces slumping are not supposed to glow) and one of the 12" paislies had begun to puddle towards the middle of the mold. The glass, you see, is *fused* at 1440 degrees. I almost never go as high as 1465 for anything, much less slumping.
The best that will happen is that everything will be a bit more slumped (puddled) than I intended, but will not be too noticeable with the organic edges. More likely, if I am really lucky, I will get the additional slumping along with some kiln wash stuck to the bottom of the dinnerware and the paislies. The penultimate worst case has the ceramic board stuck to the bottom of the Seder plates and the molds ruined, but the pieces ok. The ultimate big-time bummer has the pieces all too slumpoed to salvage and the Seder molds ruined. This would be exceptionally bad as I am out of one of the frits (crushed glass) I need to do the dinnerware commission and would have to crush some of my own in order to re-create those pieces. I would also miss my deadline for delivery of the Seder plates to the Jewish Museum of New York.
Positive karmic thoughts and prayers would be really nice right about now.
Beaten Into Submission

Kilnformer extraordinaire Bill Zweifel counseled me on the benefits of the three-hour top temp hold for the slump at the BMAC this year, and I just.cannot.make.myself do it! Barb, I know you slump the same way, and I should probably have patience and try it, but I just keep thinking that if I don't up the temp a bit, the glass will never fall.
Last night I thought I would be tricky and stack the deck in my favor. Instead of slumping onto the 1" thick ceramic board on the floor of the kiln, I put a 2" vermiculite board on top of the ceramic board just where the Seder plates would go. This means that the pieces were 2" closer to the elements which makes them slump better. (I catch myself in the use of the word "better" there. Technically it is not necessarily "better". It is faster, and as we have determined above, faster is not always better. Faster can cause your edges to pull in and up and your piece to deform.) However the Seder plates were not the only pieces slumping in Bertha last night, and I did not want the others to overslump during this intensive slump cycle: They were in taller molds and therefore initially closer to the elements.
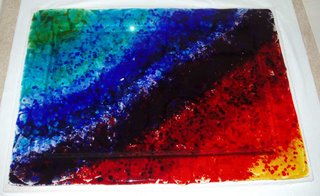

So today I will slump the second Seder set and a miscellany of other pieces, and I will ship it all out tomorrow. Three new gallery orders down and ten to go.
Monday, March 13, 2006
A molding I will go...
I think I finally have Big Bertha whipped into shape. My firing this weekend was just about perfect with a top hold of 1440 for 17 minutes. The right side is still cooler than the middle or the left. I am tempted to get a fan for more even heating (and better dispersal of the thinfire burnoff which devits the bottom of Bullseye opals if I fire with the lid tightly sealed). But I do not have the margin right now for any more kiln maintenance.
Today I cut the final molds for the seder sets and begin slumping them. And I am in a quandry on this one: I have enough new ceramic board to cut two full mold sets (14 pieces). However this may be a one-off project as they may never order them again (even though I am not charging them for r&d including mold creation these are going to be fairly expensive sets and may not sell). Cutting two full sets takes twice as much time as cutting one (duh)--a not inconsiderable amount of time--and will just about use up my one remaining sheet of ceramic board. However I do not even remember where or when I bought that ceramic board so it's not like I have a lot of demand for it...
On the other hand, if I cut two sets I would be able to slump all of the pieces today in Big Bertha instead of over two days in the medium kiln and then I could ship tomorrow--three days early--which would really please the client. Of course if I got up really early tomorrow I could do the second slump (the first being done today) in the medium kiln and get the pieces out by late afternoon tomorrow with just the one set of molds...
It's only Monday morning and my brain hurts already. I guess I will just cut the first set, see how long it takes, and if it is a real pain to cut, I will only cut one and do an extra firing. I am cutting one-piece molds for all the pieces this time because even though they are more difficult to cut, they are easier to use as they do not have any seams to fill. Today when I cut I will wear gloves (and a dust mask, of course). That ceramic board really makes me itch after no time at all.
Saturday, March 11, 2006
The Little Plate from Yesterday

It's the weekend so I got a real breakfast this morning: Dave made waffles and bacon and served them with fresh berries, coffee and oj. Yumm. I am culinarily spoiled.
Now I have to put a load in Big Bertha, wrestle with her firing schedule and beat it into submission, and deliver to Creative Spirit Gallery here in Decatur. Becky has been patiently waiting for me to bring back all the work I took for the Buyer's Market show in Philadelphia (and she has a big commission check for me--makes a Saturday delivery worthwhile!).


Friday, March 10, 2006
A Technical Post for Kilnformers Only
Coffee in the New York Skyline mug, the iPod song WAS Natural Beauty by Neil Young from Harvest Moon, but I decided I would probably slit my own throat if I listened to it any longer and switched (almost purely randomly) to Riding the Storm Out by REO Speedwagon. My husband is fond of saying the golden age of rock 'n' roll is 16 and today I am just proving him right...
Yesterday I made my first pass at slumping pieces for seder sets. I have been commissioned to do two of these sets and am finding interesting challenges. The thickness of glass I am using is 1/4" to 3/8" (more than two sheets of Bullseye and less than three) as I am using frit and every piece comes out slightly different in thickness. The parameters of the commission are to make a base plate with about a 1-1/2" rim and six smaller plates--each with a rim--which should fit inside the big plate. The little plates should be about 4" X 4" square.
I initially figured that the base plate should be 16" X 12" and I planned to use mullite (clay) shelf segments as the mold material. Yesterday I was rummaging through my stuff and I found some duraboard (ceramic fiber) pieces from old kiln lids and shelves and decided to try them first. Duraboard is a relatively soft material that can be cut with a utility knife, smoothed with sandpaper and has a fine grain for smooth detail. Mullite is very hard--I cut it with a tile saw and would need to use one of my diamond grinding bits for glass to round the top edges down.


For the glass I used scrap from a large piece that I did last summer and cooled too quickly causing it to break. (It is a sad thing when you have pieces of glass lying around which qualify as "scrap" and which are over 16" X 12".) However I made a serendipitous error in cutting the scrap: I ignored the measure twice, cut once principle becasue I was in a hurry and ended up cutting the big plate 15" X 12". You will see the serendipity of this error in the slumping result.
Into Big Bertha they went with two other large pieces and I extended the slump at the top by 10 minutes (1225 degrees for 15 minutes). The results were less than successful. Only one piece fully slumped even with the extended time. As one of the other large pieces (the control group if you will) did not fully slump either it is clearly not just the new molds (more fun with Big Bertha's firing schedules)--though they presented their own issues. It has been almost two years since I made molds like this for a dinnerware commission and for an Ikebana dish and I arrogantly forgot the lessons I learned that time.
Most molds for slumping glass have a slope to them--they do not just drop off abruptly as glass does not like to just drop off abruptly. So when you make a mold like I did you have to figure in the width of the slope (key when you are counting on a particular surface area inside the plate to put food or other little plates on). The actual flat surface size in the bottom of the big plate turned out to be just under 7" X 11"--Probably not big enough to hold the six 4" X 4" plates.

I take away from this experiment a comfortable guess at the ratio between width and height as 2 to 1 for glass of a thickness 1/4" to 3/8", and a conservative estimate of 2.5 to 1.

Now I have to redo my size calculations completely. The 1" drop on the large plate did not add to the balance of the piece and adds unnecessary complications so I am going to decrease it to 1/2". I will leave the rim at 1-1/2" for that piece. For the little plates I need to increase the rim size to 1" and I will need to see what this does to the interior flat base of the plate--it might not be balanced anymore at a 4" total size. If I have to increase the size of the small plates for balance I will also need to increase the size of the big one.
Passover is coming. I better get a move on.
Thursday, March 09, 2006
Chugging Along... Nothing Big.
So yesterday's firing was a success. The same slightly-longer-than-usual schedule that I had been using in the kiln prior to the addition of the new lid produced exactly the same results with the new lid. So today I make seder plate molds and slump a bunch of stuff. Tomorrow I ship out a load to Florida and two more will go out Monday to Wisconsin and NYC. Tomorrow I will also deliver the three pieces given away at Jessie's pre-school auction last weekend and *finally* deliver my consignment pieces back to my two local galleries.
Of course that means I have to sort through all my work today and divvy it up. I don't know why I have been dragging my feet on that task. I know why I have been recalcitrant about getting the bills out (BORING), but sorting and divvying means touching, stroking, admiring pretty pieces of kiln-formed glass. There is no bad there. There is also no available surface on which to do the divvying either as the studio is a MESS! I need a shed so the garage can officially become Studio 2.
Wednesday, March 08, 2006
The Kiln is Almost Done
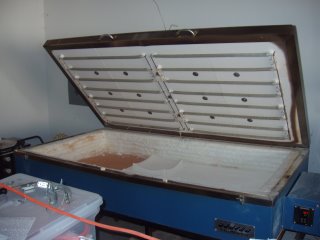
Now I blog, get caught up on bills and finances and I wait for the Maytag repairman to get here and Fix My Washer! Waiting for servicemen, like Godot, is a whole 'nother topic and gets its own post later on Stranded in the South. The iPod keeps me company as John Mellencamp is introduced by They Might be Giants and followed by the Midgetmen. It doesn't usually take me three songs to write a paragraph, I must be off my game and still in the timeslip from the other day.
Monday ended with three impossible tasks crammed into one little hour and as I am not Dr. Who and have no Tardis, they did not get done. Yesterday morning bright and early my new next-door neighbor Shane and his brother-in-law Roy came over and spent almost the entire day putting my new kiln lid on for me. It turned out to be quite a chore as the kiln was missing the four posts for the lid clamps and the electric box on the top middle was too large to fit between the steel framing from the old kiln. The framing is necessary to keep the lid from warping at high temps so I ran it around the corner to my local body shop and paid $75 cash for a piss-poor un and re-weld of two joints. I hope they are better than they actually look as the welds need to hold the weight of the lid on my counterweight system...
So far a boring, technical post and it reflects a tedious, boring day. There were two bright spots in it (or one bright spot and one really surreal spot) and they are Stranded in the South today as they are not glass related. For glass related, the Jewish Museum in New York is getting anxious for their Seder sets, I haven't finished the last two pieces of the dinnerware commission yet, I have yet to sort my inventory for shipment to distant and delivery to local galleries, I am at least 30 days past due on paying some bills--due to time and not financial constraints thankfully, my website is still really dismal (untouched), and the book? Well, at least that one is not my fault: I am STILL waiting to hear back on the *contract* edits I sent in before going to California two weeks ago.

I debated doing a test-fuse today, but the controller did not change, nor did the size of the box or the placement of the shelves. All I have done is put in new (and probably more efficient) elements and upped the insulation so I am going to go against safest practices and jump in with a real firing. Worst case, I lose some glass and waste some time, best case, I am on-time for all of my current fusing obligations.
Monday, March 06, 2006
Late, Late, Late!
It is late today and I am dragging from too many activities over the weekend. I chauffered Jessie to two birthday parties, we attended the auction and finished up the weekend at an Oscar party that went till midnight Sunday. I am too old for this... stuff.
Now at 4:00 pm on Monday I am going to tackle uncrating the new lid for Big Bertha and getting it on and the old one off. This activity will clearly extend into tomorrow. But first I need to pack up the order for a gallery in New York so I can ship it at 6:00 pm, and I really should get the last two pieces of the dinnerware commission fusing in the medium kiln too (the clients added on another 8" plate and another 10" plate in case they break one from the set).
Clearly I am working in another dimension where time passes at a different rate. Or there is a worm hole in my studio. Or I am just flat-out delusional. Take your pick.
Friday, March 03, 2006
To Own or Not to Own...
Coffee is in the Starbucks Skyline Alaska mug this morning, and I do feel like the last frontier--or the last something. There is no music (unless you count the faint strains of "Annie" wafting down from my Mom’s room).
It is Friday. I was on vacation Monday and Tuesday. I am a small business owner: Being on vacation means there are two days when things needed to get done and nothing got done. And that is the glass half empty, some would say. I say that yesterday morning it would have been a relief to get up, get dressed and commute into a job. Working for someone else--no matter how responsible the position--never requires as much effort, energy, thought and relentless reinvention of the wheel as working for yourself does. You can (and probably do) fudge a bit to your boss about why you missed a deadline (when the real reason is that you are still in post-vacation mode) but you can't fudge to yourself. Actually, I am sure there are people who can--self-delusion is not uncommon in the population (it is common--as my mother was quick to point out when I read that paragraph to her--in our elected officials... shrubbery comes to mind). It is, however, rare among business owners of businesses which survive.
So today I looked in the kiln and the slump... wasn't. A bowl which was scheduled to be shipped to the Art Institute in Chicago today for arrival *and jurying* Tuesday had to go back into the kiln for another slump. I am not hopeful I can fire and ship it today, but I will try to remain optimistic. Worst case, I can probably mail it through the post office tomorrow. (I have to work Saturdays, why can't UPS?!?). That makes the second firing this week that did not complete successfully in Big Bertha. I have the new lid for her (which has been outside still in the crate in the rain sometimes covered by plastic, sometimes not for the past month and a bit) and will probably need to get it unpacked and installed on Saturday--before the birthday parties, school auction and Oscar-filled weekend... I may have to break into some of the wine we schlepped back from California. I knew it wouldn't last.
Last night I wrote letters, updated mailing lists, mail-merged and packaged up catalogs and price lists till 11:30. Doing the small business owner marketing thing, I looked up all the galleries which purchased from me last year at the BMAC shows--none of whom I saw this time--and sent them "hey I missed you at the show" letters and packets. Yep, that's right, I am soliciting MORE work. I felt like just skipping it, but that would not be the responsible small business owner thing to do. Yes, I have a lot of production work now and through the middle of June, but eventually I will be ready for more (unless I have slit my throat between now and then) and my work has to stay vibrant and exciting in the minds of my clients in the meantime.
So I'm off to mail packets, create spreadsheets of work schedules, unpack a shipment from Bullseye, unpack from the BMAC, inventory the finished pieces I have and schedule them for re-delivery to the local galleries I emptied before the BMAC, and prepare for a big week of firing next week.
Wednesday, March 01, 2006
March already, hoo boy!
I sent my final edits to the book contract back to the Publisher the evening before I left and I still have not heard back from them. I must say, for a company which is hot to have material from me by August 15th they are sure slow to get things back to me.
Today I also begin processing orders from the Buyer's Market and preparing for a glass show at one of my local galleries at the end of the month. No rest for the wicked.
Finally, in a fit of mother-guilt, I donated a "Weekend in the Studio" to my daughter's pre-school auction fundraiser. It is an introduction to kilnformed glass for two, two projects per person with all materials and tools included. I must be out of my mind. The school was excited enough that it is one of the items in their live auction rather than the silent auction. Pilchuck it may not be, but I will still sit in the audience and pray somebody bids on it. The auction is this Saturday, squeezed between two children's birthday parties and the Oscars. No rest for the wicked indeed.